Shock Test
MIL-STD-810 F/G/H — RTCA DO 160 G
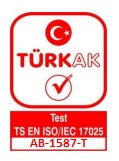
Shock Test is performed to determine the structural strength and weak points of the design under the dynamic loads to which the sample is exposed under real working conditions.
Shock testing of products is a critical testing procedure performed to evaluate their physical and functional durability against potential force impulses and temperature changes in handling, transportation and service environments. This testing determines how products respond to relatively infrequent, short-term and moderately high-level force impulses, accelerations or decelerations, and temperature changes.
Mechanical shock testing usually involves subjecting a tester to sudden and extreme acceleration or deceleration. This testing is performed using instruments such as strain gauges, load cells, piezo sensors. The purpose of the test is to measure how the device handles these situations. Multi-channel data acquisition systems use this sensor data to produce waveforms, spectrum representations, and documentation. Engineers then analyze the recorded response, determine performance and make improvements.
Mechanical shock tests are applied to examine the reactions of machines and equipment produced in the aerospace, defense and automotive sectors to shock vibrations. These tests emphasize the importance of knowing important parameters such as maximum acceleration values, shock wave length and time to reach maximum acceleration in order to simulate the real shock characteristics of the machines produced.
Shock testing is performed to determine whether products can withstand high G force and short-term impact loads. This test is important in determining the level of fragility of products, it is especially critical to know how durable they will be during transportation and positioning of military materials.
Shock tests of products evaluate the damage that various shocks may cause to materials. These tests help prevent future damage and harm by determining the conditions to which products will be exposed during the design phase. These accelerated tests are used to verify the potential lifespan of the design and the intended use of the product.
For example, shock tests to verify the ability to survive a crash inside the vehicle, under transport conditions or in normal use, significantly increase the reliability and durability of products.
Standards and Methods
- MIL-STD-810F Method 516.5
- MIL-STD-810G Method 516.6
- MIL-STD-810H Method 516.8
CONTACT BY EMAIL
[email protected]
VOICE COMMUNICATION
+90 (312) 905 06 90
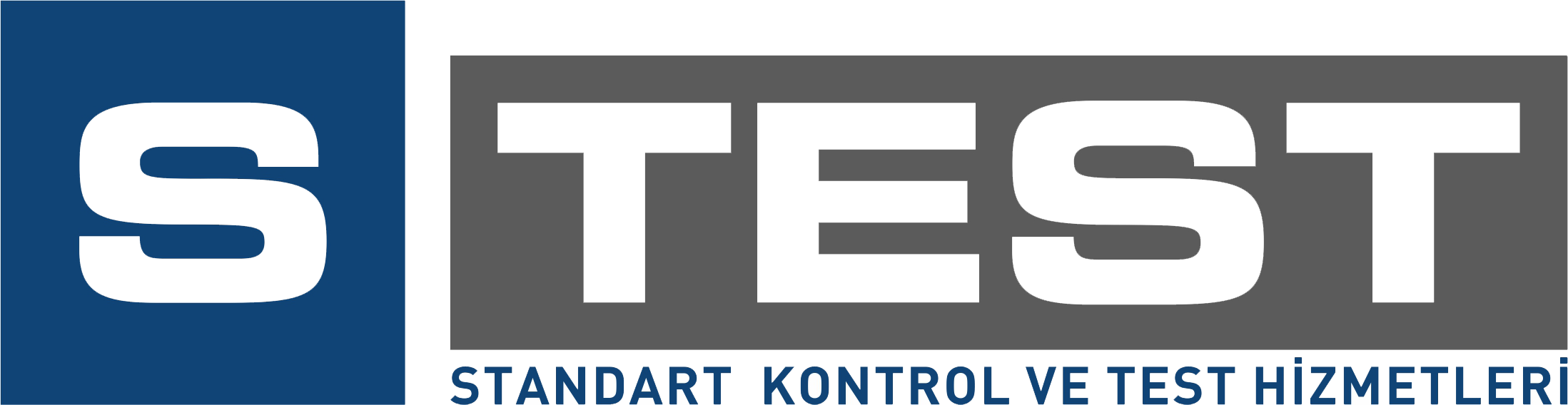
STANDART KONTROL VE TEST HİZMETLERİ A.Ş.